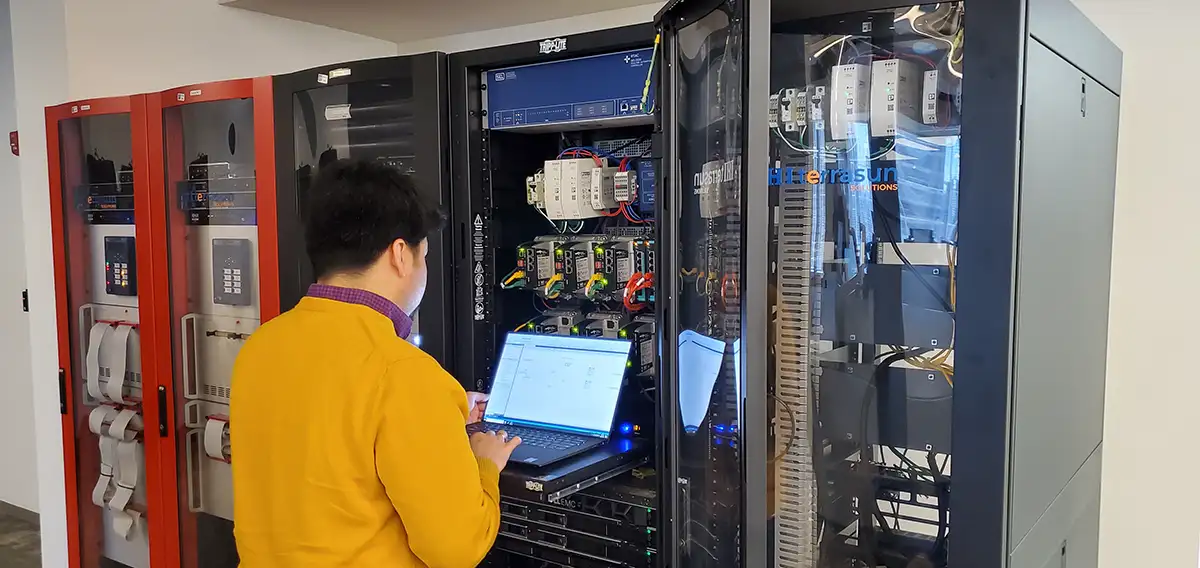
Simulation of energy storage projects reduces commissioning risk and time
Financial risk due to uncertainty can build up quickly when investing in large-scale Battery Energy Storage Systems (BESS) projects. Project execution delays, supply chain issues, and commissioning problems all are contributing factors that drive up costs and drive down viability of projects. IHI Terrasun’s simulation program reduces the risks by testing the system and identifying potential failure points prior to project installation.
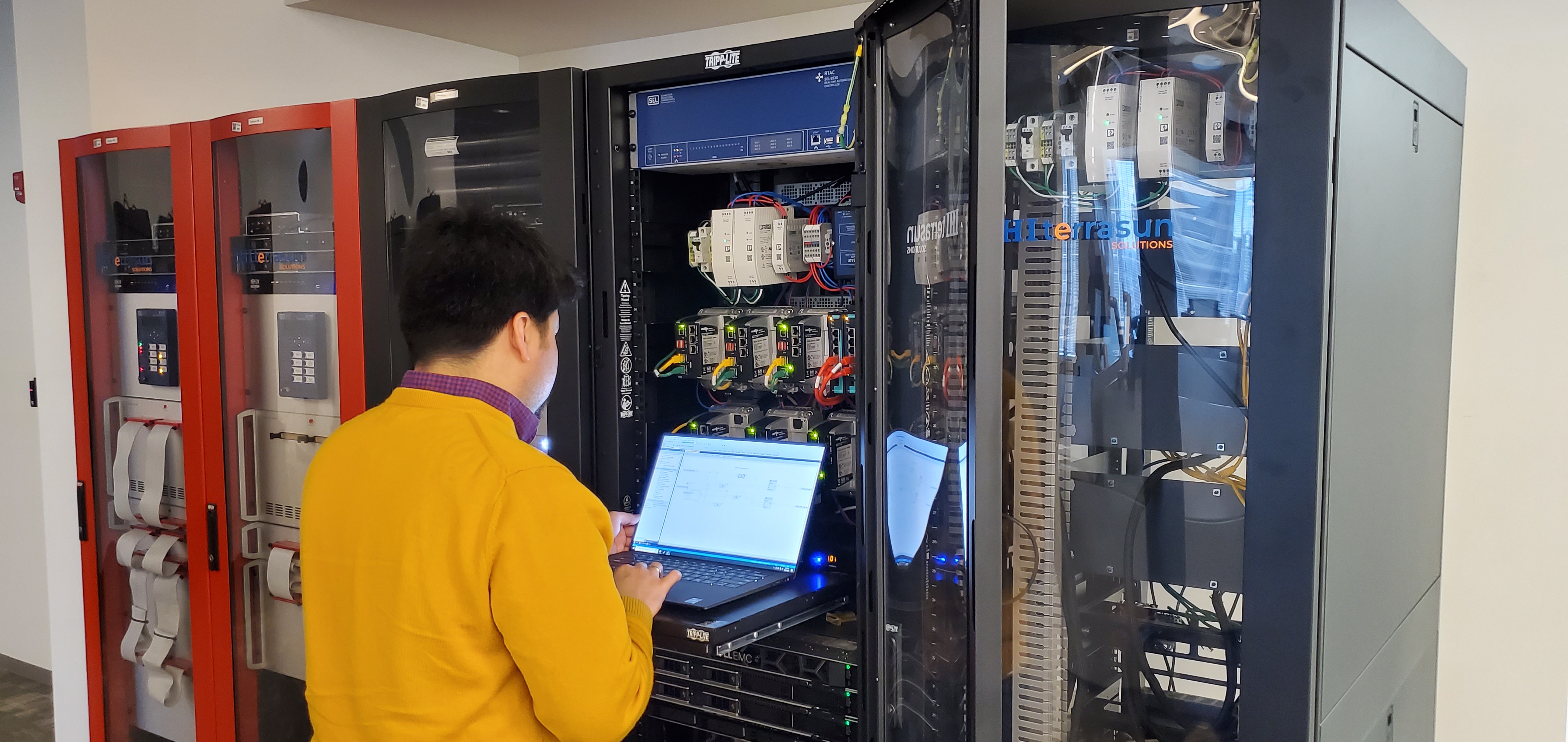
There are a few common ways to mitigate project design and operational risks before commissioning starts. Different simulation environments allow testing with different tradeoffs for cost, safety, and accuracy, which is why a robust simulation plan should include multi-faceted testing that ranges from the easily repeatable and automated to the difficult to automate, but highly accurate. Software-Only, Lab Testing, and On-Site Testing all are common methods for evaluating performance and IHI Terrasun can perform all these common methods, but each have their strengths and weaknesses:
- Software Only testing is inexpensive but is only as accurate as the equipment specifications and understanding of the system, which may not align to real system performance.
- Lab testing can provide accurate results but can only be done on a small amount of equipment. Labs also require real estate allocation and expensive dedicated systems, which may or may not be easy to reconfigure for different projects.
- On-Site Testing: Site equipment testing gives the real system responses but prohibits accurate fault simulation because of the risk of damage to equipment and system downtime. Site test is also the most dangerous and costly, as the energy transferred is real and not simulated.
There is a fourth option, IHI Terrasun’s SAFEtm (Simulation Acceptance and Fault Emulation) testing program. SAFE testing leverages Terrasun’s 7years of experience and a library of models for projects we’ve integrated and tested to create an advanced Hardware in the Loop (HIL) simulation capability. This bridges the gap between software-only and lab-scale testing, using the automation and flexibility of software simulation with the accuracy and performance of real project hardware. Typhoon HIL systems enable microsecond-level electrical simulation between real control boards from batteries, inverters, and meters and IHI Terrasun’s Rockwell Automation power plant control hardware. They provide the communication bridge between battery management systems, inverter controls, and meter readouts, system faults and alarms and the power plant controller’s software logic. This not only allows real-time simulation of typical operations, but also provides a sandbox for testing system responses to electrical and communication faults, evaluating behavior across different functional modes, and diagnosing problems encountered in system operation. Since the HIL system can simulate high impact fault conditions, such as over temperature faults or IGBT failures, there are no impacts to real hardware or personnel safety while performing these tests. Our field services team is also able to utilize the HIL simulation capability to support advanced troubleshooting and validation of any software updates before they are rolled out into the field.
The combination of IHI Terrasun’s experience and multilevel testing capability in a variety of simulation environments greatly reduces risk to the project and increases operational certainly for the power plant owners and operators. A vetted and verified equipment library from previously completed projects also gives our team the ability to combine different components for new projects quickly and easily for our customers. This agility lets IHI Terrasun predict and prevent problems that can arise in operation without having to risk damage to customer equipment or expensive downtime.