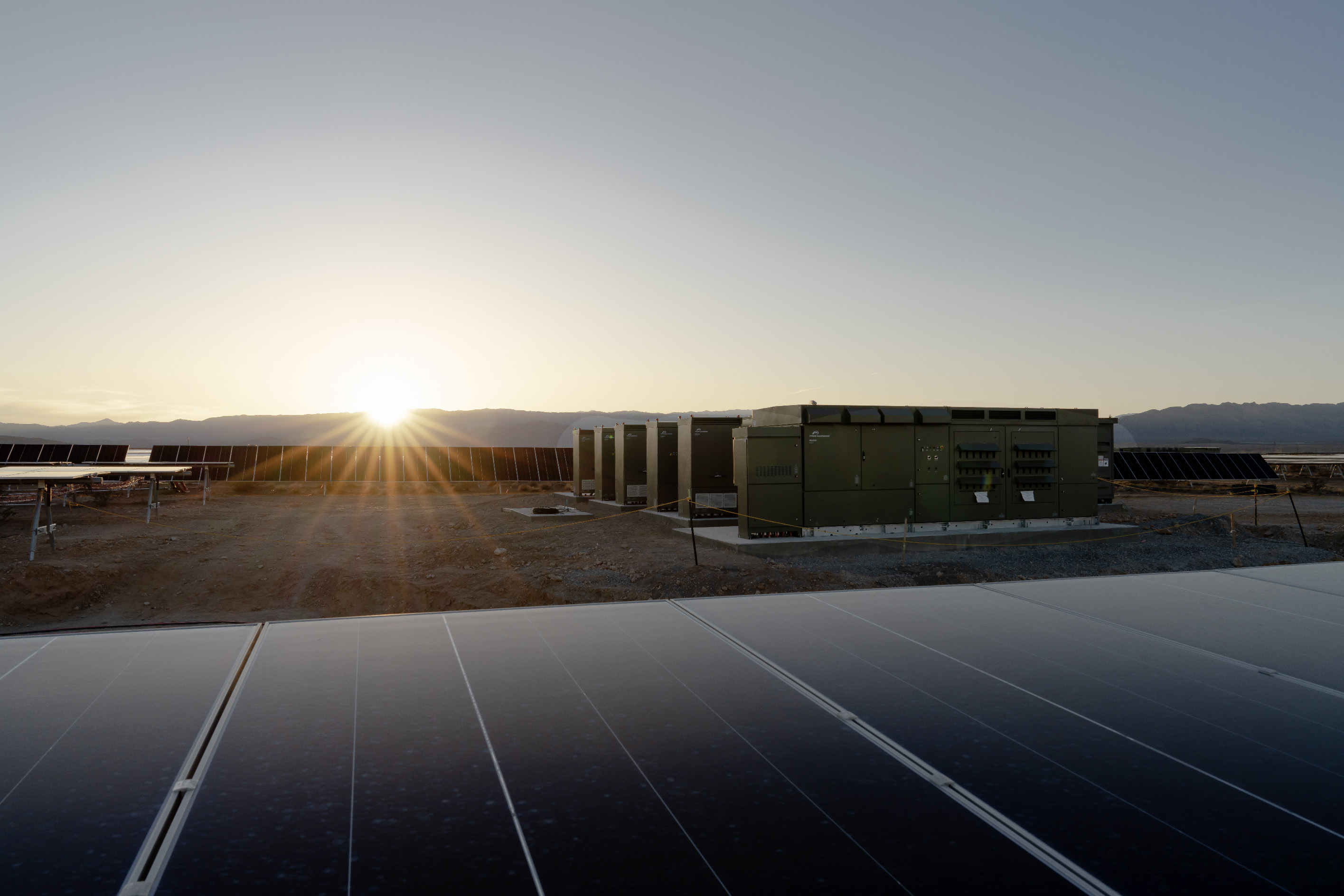
Grid reliability hinges on simulation and testing of IBRs functions
While the power plant controller is the “brain” of the BESS, the inverter included in the system determines the ability of the renewable energy project to perform grid functions and continue operation through grid disturbances.
The capability of Inverter Based Resources (IBRs) to continue operation during a grid disturbance – known as Fault Ride Through (FRT) - has been a topic of discussion since the beginning of solar power plants in the 2010s. Since then, IEEE1547 grid connection requirements for inverters have adopted changes as well as North American Electric Reliability Corporation (NERC)'s PRC-024-1 (then 2, then 3...) providing further guidance to FRT capabilities and requirements. As of 2022, IEEE2800 has essentially provided deeper guidance on FRT capabilities and the need to ensure that these capabilities are strictly enforced.
It's important to note that even if the inverter Original Equipment Manufacturer (OEM) has specified their capabilities on FRTs in their specification and literature and have provided PSSE (Positive Sequence Models) and/or Electromagnetic Transient (EMT) models, it doesn't necessarily mean that the system will perform as advertised. Even user-defined models provided by vendors may not always operate as provided. It's very important to accurately depict the models to support the reliability of the overall grid system because energy storage power plants are meant to support the grid. If the resource is out of service due to a transmission fault and the system can't ride through that scenario, it hampers operation of the whole grid sector.
While FRT may get more attention on the inverter AC side effects, an integrator must also consider DC voltage conditions. In a typical 1500Vdc Photovoltaic (PV) system the Vmp will typically operate a maximum around 1300Vdc, so rarely would it go up to its maximum 1500Vdc. Hence, there is quite a bit of headroom in terms of voltage tolerance. For BESS, almost all 1500Vdc batteries connected in series will operate up to 1450~1490Vdc. Thus, there is very little headroom in the maximum voltage area when the battery is fully charged. Having an AC grid event that may affect these limits shows why DC & AC systems need to be verified. For grid stability and operation, edge-cases need to be examined with a finer lens.
NERC published the first BESS Disturbance Report out of many other disturbance reports in PV and inverter-based resources (IBR). The BESS projects under review all failed FRT, taking MWs of energy storage capacity offline.
Proper modeling, validation, and testing work together to ensure that the systems deployed are reliability capable of supporting fault events. Hardware in the Loop (HIL) testing provides a pathway to truly validated models. Strong testing programs are crucial to ensure that the technology is evaluated appropriately.
Recently, I joined my colleague Jim Cleveland, a HIL simulation expert, and Typhoon HIL, a HIL solutions provider, for a webinar on safe and efficient energy storage system simulation that addresses this exact problem. IHI Terrasun uses Typhoon HIL's C-HIL solutions to test fault conditions on batteries and inverters, along with all inverter functions.
In this webinar, we covered a variety of topics, including:
- IEEE 2800 standard and why validation on HIL systems will be essential for meeting future requirements.
- C-HIL principals and what HIL-Compatible means.
- The application through each stage of a power plant software development lifecycle.
- The value and necessity of HIL for energy storage system integrators.
Typhoon HIL design, testing, and validation has accelerated time to market and overall project success, proving that simulation is a valuable tool in the BESS integration, leading to lower commissioning times and reducing risk. Many independent systems operators (ISOs) are also opting to adopt the IEEE 2800 standards for BESS systems in their regions. Integrators must prepare to adhere to the required standards and the developed testing methodology which is described in IEEE2800.2.
Watch the recorded webinar:
Leveraging HIL Compatible for Safe and Efficient Energy Storage System Deployment